By Jeff McClellan
The scriptures tell a story of two men–a wise man and a foolish man. The wise man built his house upon a rock, and when the rains fell and the floods came and the winds blew, the house on the rock stood firm. But the foolish man built his house upon the sand, and when the rains fell and the floods came and the winds blew, the house on the sand fell.
That’s the story, and it’s a story by which BYU’s Kyle M. Rollins stands. But at the same time, this associate professor of civil engineering is trying to make it possible for wise people to build on the sand in a way that their houses won’t fall.
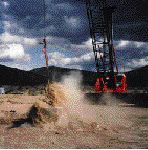
A 5-ton weight crashes into the ground just outside Nephi, Utah, where a BYU professor was testing various methods for treating collapsible soils. A common problem in the Southwest, collapsible soils can cause severe damage to structures when the rains fall and the floods come.
Much of the southwestern United States is plagued by collapsible soils–combinations of clay and sand left by mud flows that have dried, leaving tiny air pockets. When the soil is dry, the clay is strong enough to bond the sand particles together, explains Rollins. “But when the clay gets wet, it loses its strength, and this card-house structure starts to collapse in on itself.” And when collapsible soil collapses, one can imagine what happens to structures built on it.
“There have been a couple of places in New Mexico where they had a real wet season, and the governor actually declared it a disaster area–in part, at least, because of all the collapsed settlement that took place,” says Rollins. And in central Utah, a cement plant built on collapsible soils suffered more than $20 million of damage.
Such damage occurs throughout the Southwest along mountain fronts where for centuries mud has washed out of canyons and dried in the arid climate. When Rollins worked with his father’s engineering consulting firm, he often witnessed this damage and wondered at an effective solution.
So when he became a professor at BYU a few years ago, his first research project was to compare the various methods for treating collapsible soils. In November, the paper Rollins wrote about his research earned him the Arthur Wellington Prize from the American Society of Civil Engineers. The award is one of the top three society-wide awards the organization gives annually to authors of outstanding journal articles.
Unlike most people who deal with collapsible soils, when he did his research Rollins wanted to get the ground wet. So he borrowed a farmer’s field in Nephi, Utah, treated the collapsible soil in five locations with the various methods, built small foundations on the treatments, and then got the ground soaking wet.
For comparison purposes, Rollins also built a foundation on an untreated plot of ground. When the untreated foundation was wetted, it settled about 11 inches. In addition, the soil collapsed unevenly, and the foundation tilted about 15 degrees.
The first treatment method was prewetting, where a contractor wets the ground before building, hoping any settlement will take place at that time. When this method was used, the foundation tilted and settled more than 9 inches. “We found that prewetting isn’t very helpful,” says Rollins.
The second method, among the more common techniques in Utah, involves excavating part of the collapsible soil and replacing it with compacted gravel beneath the footing. In Rollins’ research, this method caused the foundation to settle evenly and it slowed the onset of significant settling. Once the site received enough water to get through the gravel and into the soil, however, the foundation settled about 4 and one-half inches.
Treatment with a sodium silicate solution was the third method. Poured into small holes drilled in the ground, the solution seeps into the soil and creates a cementing effect. This treatment limited settling to about 1 inch.
The final treatments involved dynamic compaction, where a large weight (between 4 and 30 tons) is raised by a crane to between 50 and 100 feet and then dropped on the ground. The weight is dropped several times on one spot, creating a crater about 4 feet deep. After the process is repeated in several locations on the site, a bulldozer levels the ground. In effect, the process creates columns of compacted soil throughout the building site.
In Rollins’ research, he tried the dynamic compaction treatment on both wet and dry ground. The results showed the dry compaction to be slightly more effective, but the settlement for each of the methods was minimal–less than one-half inch.
“The dynamic compaction, although it was a little more expensive than the other treatments, was far and away superior in terms of the settlement that took place,” says Rollins.
He says dynamic compaction would be most cost efficient when a large area of ground is being treated. “It would be difficult to justify it for one house.”
Rollins has continued his studies with dynamic compaction, looking at ways to make the treatment more effective and economical.
In his presentations about dynamic compaction, Rollins says he likes to point out that he’s not the first person associated with Brigham Young to use the treatment. The first known use of dynamic compaction was when the early Mormons filled a cannon with lead shot and, using mule teams to hoist it, dropped the cannon several times to improve the ground before they built the St. George Temple.