Pattern This prototype design is based on the origami flasher pattern, which is used as a basis for both reflectarray antennas and lidar-telescope apertures.
35 joints allow the panel to fold. Each joint uses thin metal strips to allow a wider range of movement.
140 high-force magnets stabilize the array when it’s deployed.
2.5cm Thickness of the meter-wide prototype. In gravity-free space, however, the actual array—a compliant mechanism—will be thinner.
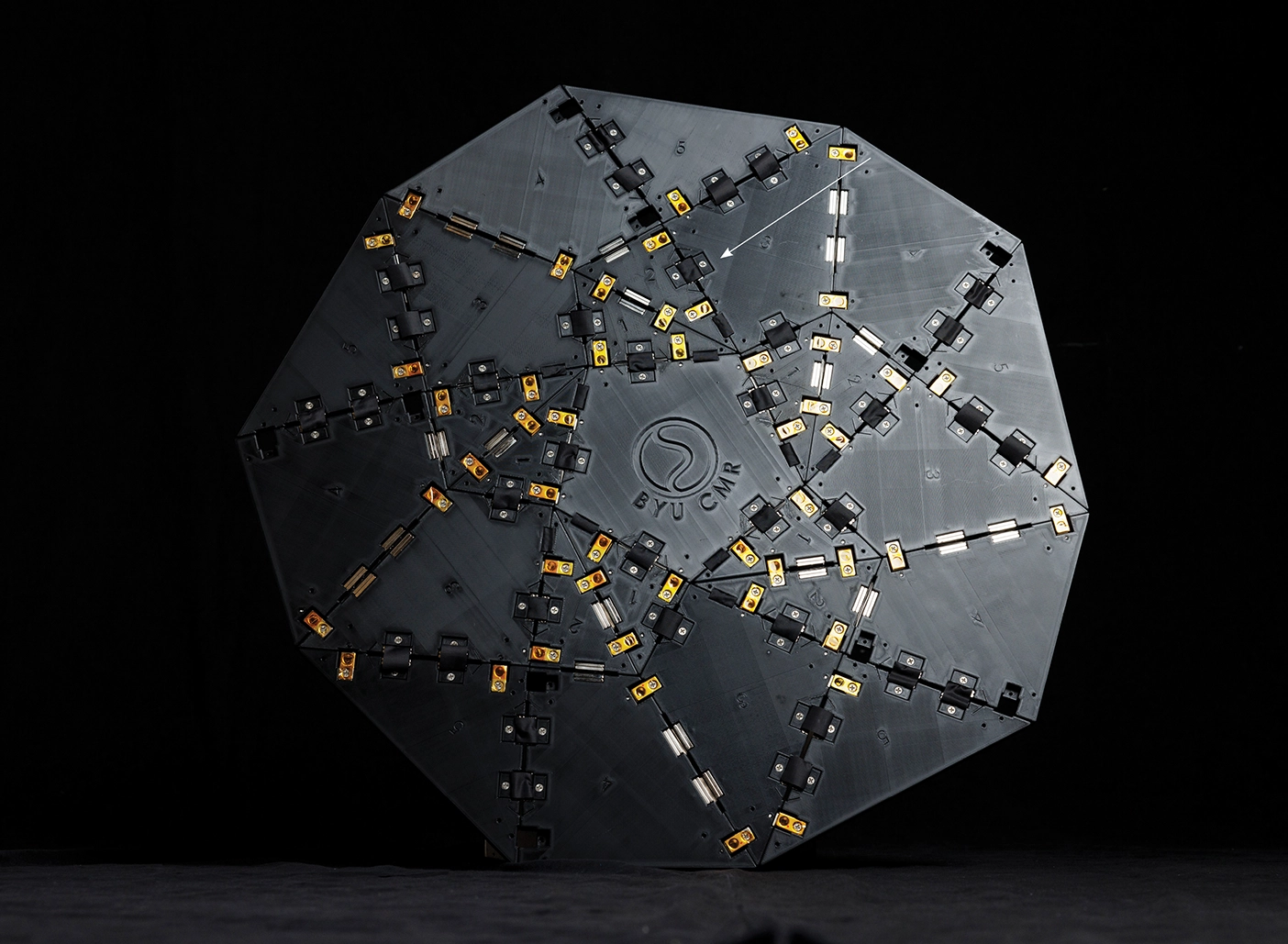
In the grand expanse of outer space, humanity’s efforts to communicate and capture signals depend on the size of our technology. The bigger the array or telescope, the better the capabilities. However, larger structures are more expensive and challenging to deploy. Mechanical engineering professors Larry L. Howell (BS ’87) and Spencer P. Magleby (BS ’83, MS ’83) led the Compliant Mechanisms and Robotics Lab in creating origami patterns to keep space technology compact and affordable. The prototype pictured is an initial conceptualization of these origami-inspired patterns. It’s “just one piece along a long pipeline that would eventually lead to flyable hardware,” says Magleby.
Work on these systems has been funded by the Air Force Research Labs and NASA. The lab recently published on magnetic stabilization, the system used to flatten the prototype when it deploys. The 25-year collaboration between Magleby and Howell in the lab is “one of those things where we have accomplished much more together than we could have individually,” says Howell. The spiritual foundation of BYU has been integral. “One of our jobs as children of God is to understand the universe,” Magleby says. “The technologies we’re developing here will eventually let us look at this immense universe more carefully. It’s an awesome world, and we’re just playing around in a little teeny piece of it.”