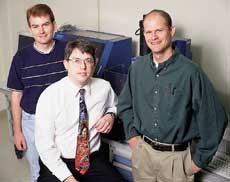
In the last three years, BYU has filed patents for eight compliant (i.e., flexible) mechanisms invented by Larry Howell, associate professor of mechanical engineering (seated), and his students, including Scott Lyon (left) and Gregory Roach.
By Mary Lynn Johnson
Lots of BYU students ride their bikes to class. But for mechanical engineering alum Todd R. Coons, riding to campus was sometimes pretty serious research. Back in 1996, Coons and classmate Elijah B. Garner designed a bike brake that, after a few years of refinement, is now on the market. Using technology pioneered by associate mechanical engineering professor Larry L. Howell, the students found a way to simplify a popular brake design in ways that improved both wear and price.
The brake began as a class project and, like most of the work done in Howell’s research group, it applies the theory of compliant mechanisms. The idea is to simplify everyday devices by replacing their joints or hinges with flexible materials. “We get our motion from the deflection of flexible beams,” Howell explains, “rather than traditional methods like movable joints.” So far he and his students have filed full or provisional patents on eight different inventions, including new incarnations of an all-purpose switch and a small-motor clutch, in addition to the bike brake. More inventions are on the way.
According to Howell, the potential advantages of compliant mechanisms are many. If a joint can be replaced with a flexible beam, chances are the product will need fewer parts and less assembly time. It will also likely cost less, weigh less, make less noise, require less lubrication, and last longer.
There’s just one major drawback, however: such gadgets are reallyhard to design.
The analysis required for making compliant mechanisms is usually far more complicated than that for mechanisms with only rigid parts, Howell explains. In fact, during his PhD study at Purdue University, he was told that nothing practical would ever be designed using compliant mechanism theory.
“People told me that you couldn’t design a compliant mechanism to do even a very simple task because it was too complex,” he says. “But through a lot of very fortunate things I discovered a way to model the analysis and make it fairly straightforward.” Howell’s “pseudo-rigid-body” method for modeling compliant mechanisms helped win him a National Science Foundation Career Award in 1996.
Compliant mechanisms don’t typically employ materials the average consumer would consider elastic. In fact, they are routinely made from steel and other metals. Flexible beams of stainless steel are key features of the bike brake, the first BYU-designed compliant product to reach a mass market.
Even with Howell’s guidance, Coons says, the brake project was tough. His team’s first brake-making efforts were a mild disaster—an early prototype snapped right after it was made. Still, by the end of the semester they had a rough brake that would stop a bike.
Though the class was over, Coons wanted to take the project further. With a grant from BYU’s Office of Research and Creative Activities and under Howell’s supervision, he pursued the project on the side while earning his master’s degree.
“I loved it because I found myself using all these things that I learned in school,” says Coons, now a mechanical designer at Pratt and Whitney in Connecticut. “I could measure deflection and force and see if the equations equaled what the brake did in real life. Seeing the theory and the engineering work in reality was neat.” When they finally achieved a successful design, Coons put the prototype on his own bike and rode it back and forth to school.
“I didn’t ever suspect that we would patent it or that anybody would buy it,” he says. But one day Howell suggested that they show the invention to someone in BYU’s Office of Technology Transfer, which funnels campus-created technology into for-profit industry. Armed with drawings and models, technology office staffers took the brake design to an industry convention, where it sparked the interest of representatives from Tektro, a Taiwanese manufacturer of bicycle parts. Within a year the brake was in stores, mostly on BMX bikes.
While it’s a nice side effect, success in the market was hardly the point of the research endeavor. In fact, if and when BYU-designed compliant mechanisms show up on retail shelves, they won’t carry any reference to BYU. The licensing agreements require that manufacturers not use the university’s name in any of their advertising or promotions.
For Howell, the achievements of his students are far more important than sales or recognition. “At other schools you can’t find this many patents or products coming out,” he says.”And one of the reasons we’ve been successful, I think, is that one of my goals was motivation of students. With the students here, we’ve built a program that is second to none in what we do. We’ve got some very sharp students.”
One of those students is Gregory M. Roach from Springville, Utah, who has been part of Howell’s research group for the last three years. While earning their master’s degrees at BYU, Roach and Scott M. Lyon, both now PhD candidates in mechanical engineering, designed a compliant, overrunning ratchet-and-pawl clutch comprised of only two parts and one pin. It’s the kind of clutch found in garden tools like WeedEaters, Roach says, and “the beauty of it is that it retains all of the functionality without all of the extra parts.” In 1998 their clutch won first place in the graduate division of the American Society of Mechanical Engineers’ National Mechanisms Design Contest, and the article they and Howell wrote about the invention won a best paper award from among more than 100 papers submitted in their category. Przybyla is now promoting the device.
Roach also helped to design the switch BYU has patented. With Howell and Brian D. Jensen, now an engineer at Sandia National Laboratories in Albuquerque, N.M., he created a one-piece, compliant switch that could one day be used for common light switches or circuit breakers.
“Compliant mechanisms aren’t the holy grail answer to everything,” admits Roach, who manages BYU’s new Utah Center of Excellence for Compliant Mechanisms, a product-development effort funded by the state of Utah and directed by Howell and associate professor of mechanical engineering Spencer P. Magelby. But in certain applications—like the bike brake, where production costs were cut by two-thirds—they make great economic sense, Roach says.
Roach and Coons agree that while student inventors do receive royalties for their products, they get a far greater payoff in experience and pride.
“You get all these skills in the classroom, and this is an opportunity to do something practical with them,” Roach says, “to see the process through from the beginning concept to a product that’s being used. You can go buy it if you want—something that you’ve had a hand in helping to design.”
More information about BYU’s compliant mechanisms research is available on the Internet(https:// www.et.byu.edu/~llhwww/).