BYU manufacturing professor Yuri Hovanski (BS ’01) examined mechanical arms working on the Toyota Sienna’s sliding doors. He and graduate student Damon M. Gale (BS ’23) had been invited to tour a Toyota factory, hopeful that BYU’s advancements in stir welding could improve the company’s carbon footprint. At most, their partnership with Toyota was anticipated to halve the energy needed to weld the minivan’s doors. Instead, the improvements from BYU’s research blew everyone away.
“This project really has huge environmental impacts,” Gale explains. Refill friction stir spot welding, the technique Hovanski’s team has been refining, combines two pieces of metal by stirring them together. Rather than melting the metal, as in traditional welding methods, friction stir welding uses aluminum’s pliability to combine solid metals. After the team verified their new process wouldn’t affect the speed of car production, they were surprised to see how much energy—and money—could potentially be saved.
“We have the opportunity to dig in and be better stewards of the world,” Hovanski explains. Hovanski sees the manufacturing program as a reminder that BYU students can make a difference, even as undergraduates. “Manufacturing creates an opportunity to design and implement in a way that makes a really positive impact on the world.”
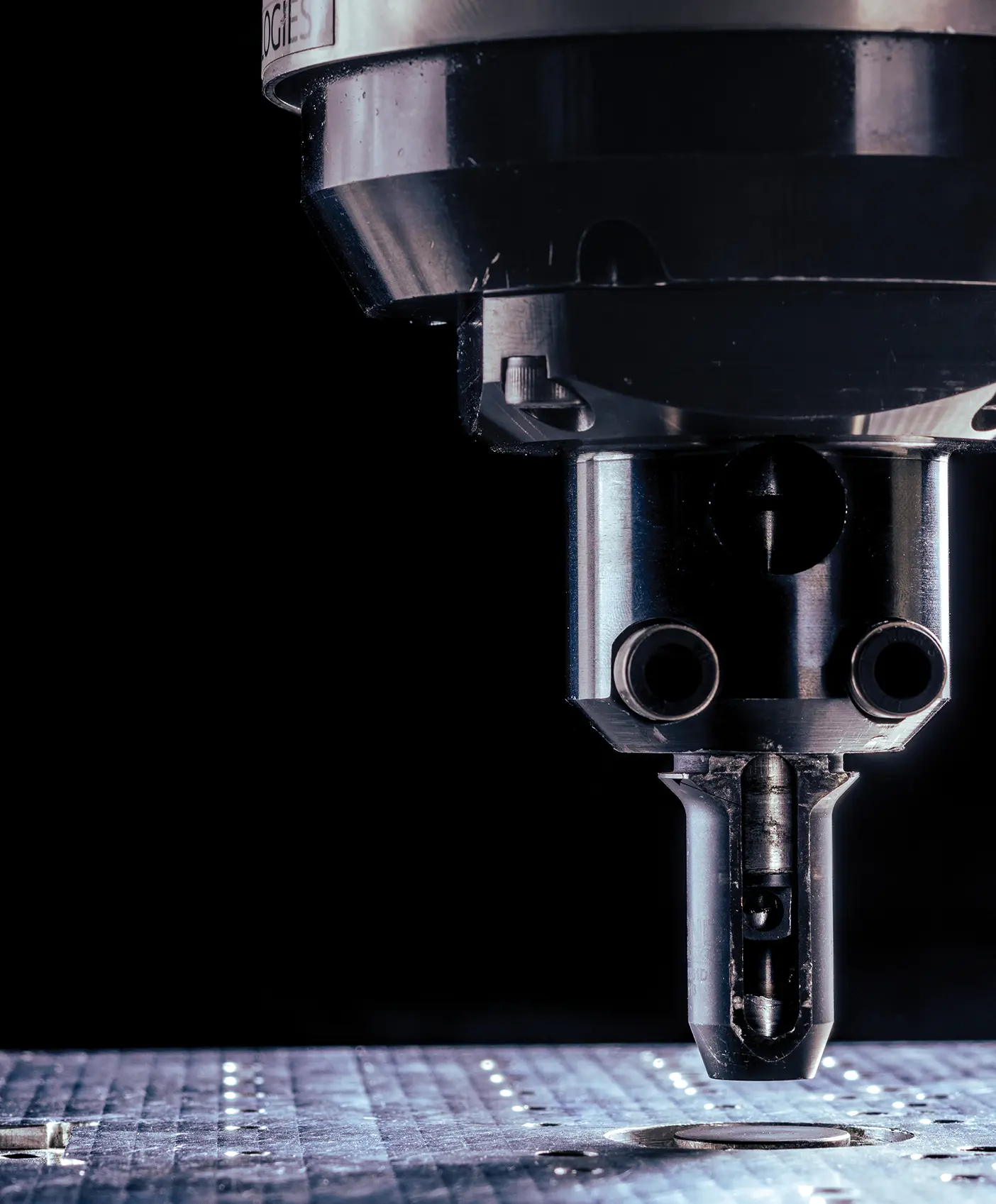
40x
less energy per weld was needed when Toyota used BYU’s technique for building minivan doors.
250,000
welds in a row without a tool change in a Toyota production line.
250 milliseconds
Time required for the friction stir welding machine to perform a weld—the fastest refill friction stir spot weld in the world. Researchers estimated a 2-second minimum before BYU got involved.